Olds leads the way as medical marijuana market booms
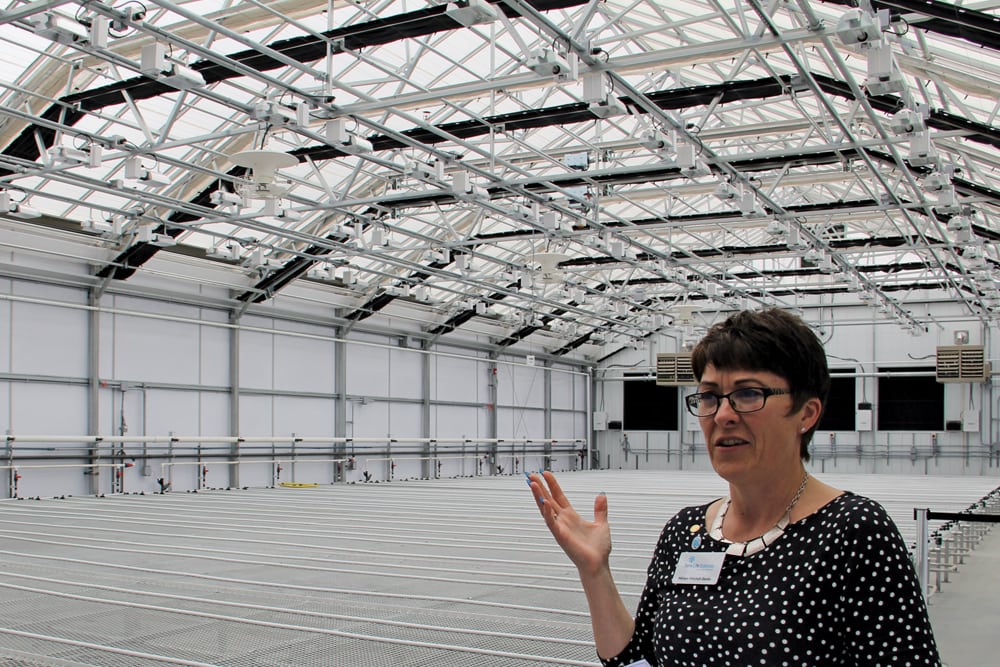
Terra Life Sciences shows the power of value-added processing in its cannabis cultivation facility and pharmaceutical plant.
Terra Life Sciences would look like any other manufacturing plant if not for the security guard parked out front.
He’s the gatekeeper here. You’ll find another one just like him at the other gate, checking in visitors, scrutinizing IDs, buzzing through the people who pass muster.
But these guards are just your first glimpse of the Fort Knox-style security system at the Olds-based pharmaceutical company. As you make your way through the greenhouse and manufacturing plant, you’ll see plenty more — hundreds of cameras lining the walls, passcodes on nearly every entryway, alarms that wail when you leave a door open a little too long.
It seems extreme, but it needs to be. The greenhouse workers aren’t growing strawberries to make jam, but medical-grade cannabis and drugs.
“It’s like a bank vault. It’s 100 per cent secure,” said Anil Jain, president and CEO of Terra Life Sciences. “I don’t even have security clearance for some parts of the facility.”
There is nothing in the country like his company’s new 50,000-square- foot cannabis cultivation facility, says Terra Life Sciences’ president Anil Jain.
Growing a controlled substance and manufacturing pharmaceuticals mean having a level of security that not only keeps the RCMP happy, but also Health Canada and the United States Food and Drug Administration. The latter is unusual, and requires especially stringent security and oversight, said Jain.
Then again, nothing about Terra Life Sciences is quite like its cross-country counterparts in cannabis cultivation. The company’s focus is on the medicine, not the recreational drug, and it conducts clinical trials for diseases such as multiple sclerosis and chronic pain. They produce upwards of 1.8 billion soft gels a year — and no buds.
“Cannabis cultivation is not what Terra Life is all about,” said Jain. “First and foremost, we are a pharmaceutical company making medical-grade products using actives from cannabis.”
And business is booming. In late May, Terra Life Sciences unveiled its new 50,000-square-foot cannabis cultivation facility, which will produce around 5,000 kilograms of dried cannabis a year. The next phase of the expansion will be five times bigger than that — a 230,000-square-foot facility producing upwards of 35,000 kilograms of dried cannabis by next year.
“We couldn’t buy pharma-quality cannabis from anywhere in Canada,” said Jain. “We had to cultivate our own.”
Cannabis cultivation
The production practices are just as rigorous as their security measures. Under federal regulations, the company must test for a multitude of things at every step of the way — including pests, bacteria, and fungi; heavy metals; mycotoxins; and levels of THC and CBD (the active chemicals produced by cannabis plants).
“We’re growing medicine — not plants,” said director of cannabis cultivation Dejun Cui.
“The plants themselves aren’t hard to grow. They’re very easy to grow. But if you want to pass all these tests, you can’t grow it in the field. You have to grow it in a controlled environment.”
Because of that, Terra Life’s new greenhouse is top of the line, with insulated corrugated walls and diffused glass on each of the eight growing bays.
“We built this to the standard that one would build an oil refinery or gas plant,” said Miriam Mitchell-Banks, senior vice-president of supply chain and global collaborations. “Not everybody is building to this level. We build for pharma.”
Each bay is about 4,100 square feet and can hold about 2,000 plants, which are monitored by a central computer system through sensors that measure for things such as temperature and humidity.
“The computer runs the entire facility,” she said. “It’s the real brains of the operating facility.”
But if the computer is the brains behind the operation, genetics lie at its heart.
“That’s the most vital part of this whole thing,” said Mitchell-Banks. “If you don’t have the right genetics, you don’t have anything.”
Terra Life grows more than 100 varieties of cannabis that were designed to treat chronic illnesses. And these plants all start in the ‘mother room,’ where the ‘mother’ plants are grown and then cloned.
“The mother room is our pride and joy and where we have to take the most care and attention,” she said.
Workers take clippings from the mothers, put them into propagation powder, place them into small cubes, and then transport them to the propagation room. From there, the plants grow into seedlings and are then transferred into bigger pots, where they grow into smaller ‘teenage’ plants. At that point, they’re moved into the flowering bays.
Once ready for harvest, they’re cut at the bottom of their stems and then transported by trolley to the trimming room. Not every part of the plant contains active chemical compounds, so the plants are trimmed of all the usable material — separating the ‘wheat’ from the ‘chaff,’ as it were.
“If I were the size of a plant, the leaves from the shoulders down really don’t have much of the chemicals we’re looking for, so we’ll cut those off,” said Mitchell-Banks.
“It’s the leaves around the shoulder area — the buds — that have the most chemical compounds. Those are the ones we’re going after.”
Buds are then put onto trays and taken into the drying room to reduce their moisture content down to about 12 per cent. (Despite having no active chemical compounds, the waste material is shredded into minuscule pieces and then composted to comply with federal regulations.)
Everything is then completely sterilized for the next batch of plants, and the production process begins anew.
Manufacturing for global markets
That process — from propagation to harvest — takes about three months, but the plants aren’t at the end of the line yet.
From the drying room, the buds are taken to the manufacturing facility, where they’re ground into fine powder and then packed into a two-cylinder extraction machine.
Each cylinder holds about four pounds of dried plant, which is treated with a carbon dioxide solvent. Under the right pressure and temperature, the solvent ‘gloms’ onto the cannabinoids (or the active compounds), and after about seven hours, a thick resin about the size of a cup of butter comes out.
“It’s kind of like making gravy,” said Mitchell-Banks. “When you cool gravy, the fat goes to the top. The fats and lipids in the plant do the same thing in our process.”
The resin is then mixed with ethanol, which removes any unwanted compounds (such as wax), and then further refined to remove the ethanol. The pure product — about 280 grams, when all is said and done — is either blended right away and sent to the encapsulation line, or stored in a vault for later use.
The main production facility has eight encapsulation lines that can produce around two billion soft gels a year. These soft gel machines take ribbons of gelatin and run them over specialized dies that have a series of divots on them. Each one of these divots is injected with the resin and an excipient (a neutral ‘filler’ such as olive or sesame oil), and the resulting soft gels are then dried into capsules and put into the blister packs you’d get at the pharmacy.
These cannabis soft gels sell for three times more than the plants on a per-gram basis in the global market — a boon of the value-added processing that will add not only value to the product but also an additional 150 jobs to Terra Life’s Olds’ facility over the next two years.
“With our blue skies and sunshine, Alberta is the ideal place to grow medical-grade cannabis,” said Jain. “But we will not sell cannabis flowers. We will be cultivating them, extracting them, making soft gels, and then selling them. And through this development of cannabis medical products, we intend to do our part to lead the way in this exciting burgeoning industry.
“That’s value added.”
420 Intel is Your Source for Marijuana News
420 Intel Canada is your leading news source for the Canadian cannabis industry. Get the latest updates on Canadian cannabis stocks and developments on how Canada continues to be a major player in the worldwide recreational and medical cannabis industry.
420 Intel Canada is the Canadian Industry news outlet that will keep you updated on how these Canadian developments in recreational and medical marijuana will impact the country and the world. Our commitment is to bring you the most important cannabis news stories from across Canada every day of the week.
Marijuana industry news is a constant endeavor with new developments each day. For marijuana news across the True North, 420 Intel Canada promises to bring you quality, Canadian, cannabis industry news.
You can get 420 Intel news delivered directly to your inbox by signing up for our daily marijuana news, ensuring you’re always kept up to date on the ever-changing cannabis industry. To stay even better informed about marijuana legalization news follow us on Twitter, Facebook and LinkedIn.