You are here
Home 🌿 Cannabis Technology News 🌿 Hemp, you can’t smoke it, but you can use it to build green houses 🌿Hemp, you can’t smoke it, but you can use it to build green houses
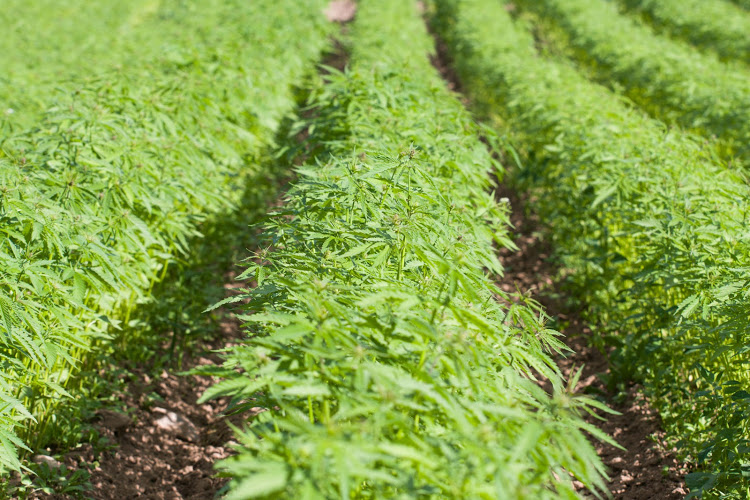
The hemp fields sprouting in a part of Canada best known for its giant oil patch show how climate change is disrupting the construction industry.
Six years after setting up shop in the shadow of Calgary’s tar sands, Mac Radford says he cannot satisfy all the orders from builders for Earth-friendly materials that help them limit their carbon footprints. His company, Just BioFiber Structural Solutions, is the vanguard of businesses using hemp — the boring cousin of marijuana devoid of psychoactive content — to mitigate the greenhouse gases behind global warming.
Around the world, builders are putting modern twists into ancient construction methods that employ the hearty hemp weed. Roman engineers used the plant’s sinewy fibres in the mortar they mixed to hold up bridges.
More recently, former White House adviser Steve Bannon weighed in on using so-called hempcrete to build walls. Early results indicate it’s possible to tap demand for cleaner alternatives to cement.
Hempcrete structures also have better ventilation, fire resistance and temperature regulation, according to their proponents
“We have way more demand than we can supply,” said Radford from his plant in Airdrie, which is undergoing expansion and soon expects to churn out enough Lego-like hemp bricks each year to build 2,000 homes.
Greener alternatives to cement add to the pressure on companies including LafargeHolcim and Votorantim Cimentos as the global economy pivots toward dramatically lower emissions.
Cement makers are responsible for about 7% of global carbon dioxide (CO2) emitted into the atmosphere every year, with copious volumes entering via limestone kilns needed to produce the material. Manufacturers say they’ve struggled to find markets for greener alternatives, giving easy entrance to entrepreneurs such as Radford, who cater to customers concerned about their impact on the Earth.
“They love it once they understand it,” said Radford of the builders who’ve adopted the modular, inter-locking bricks he invented for their projects. “Our old practices we have to change.”
Carbon footprint of building materials
While architects and developers have traditionally concentrated on the energy used by their buildings once they’re are standing, it’s actually the materials required in their construction that represent the brunt of a structure’s lifetime carbon footprint. Replacing high-carbon-intensity materials such as cement with greener alternatives such as hemp can dramatically reduce or even offset greenhouse gas pollution.
Hemp fields absorb carbon when they’re growing. After harvest, the crop continues to absorb greenhouse gases as it’s mixed with lime or clay. Hempcrete structures also have better ventilation, fire resistance and temperature regulation, according to their proponents.
Numbers across the industry vary depending on the process, but Just BioFiber says that its hemp captures 130kg of CO2 for each cubic metre it builds. Structures made with their bricks will sequester more greenhouse gases than they emit in production. By contrast each tonne of cement produced emits half a tonne of CO2, according to the European Cement Association.
First developed in France more than 30 years ago, hempcrete was initially used for renovating old houses since it mixed well with stone and lime. That has progressed to new build homes, offices and municipal buildings some as tall as seven floors, according to Quentin Pichon, founder of CAN-Ingenieurs Architectes who specialize in hempcrete buildings.
Hemp growth in France has grown by fifth in the past decade as a result of an increase in its construction use but also because seeds from the plant that can be used to make cannabidol, he said. Hemp sales in Canada could hit $1bn within five years from $140m last year, according to the Northern Alberta Institute of Technology.
That ability to quickly ramp-up local cultivation virtually anywhere in the world is one of hemp’s appeals, according to Alex Sparrow, MD of UK Hempcrete.
“Demand is rising steadily but we need to accelerate this as, currently, the UK construction industry accounts for approximately 7% of GDP and 50% of total UK carbon emissions,” Sparrow said.
One of the principle challenges his UK company faces are legal hurdles imposed on hemp cultivation — British farmers can only grow hemp building materials but can’t profit from the oil extracted from seeds.
Back near Calgary, the black denim-clad Radford is already turning a profit from his hemp venture and is preparing to invest another C$37m ($28m) to expand production to 3.5-million bricks a year. He credits his children with convincing him to go green after four decades in commercial development.
“They think that finally it’s not about money, it’s about doing good for the planet.”
420 Intel is Your Source for Marijuana News
420 Intel Canada is your leading news source for the Canadian cannabis industry. Get the latest updates on Canadian cannabis stocks and developments on how Canada continues to be a major player in the worldwide recreational and medical cannabis industry.
420 Intel Canada is the Canadian Industry news outlet that will keep you updated on how these Canadian developments in recreational and medical marijuana will impact the country and the world. Our commitment is to bring you the most important cannabis news stories from across Canada every day of the week.
Marijuana industry news is a constant endeavor with new developments each day. For marijuana news across the True North, 420 Intel Canada promises to bring you quality, Canadian, cannabis industry news.
You can get 420 Intel news delivered directly to your inbox by signing up for our daily marijuana news, ensuring you’re always kept up to date on the ever-changing cannabis industry. To stay even better informed about marijuana legalization news follow us on Twitter, Facebook and LinkedIn.